PAVIWATER® A+B
Formulato epossidico colorato in emulsione acquosa (a+b)
Formulato epossidico bicomponente colorato per rivestimenti ad elevata resistenza chimica. Particolarmente indicato per il trattamento di canaline e vasche di contenimento.
Tipologia: Formulati Epossidici a Base Acquosa
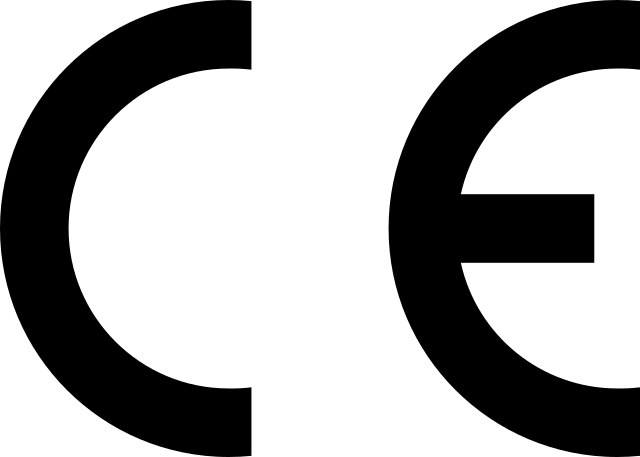
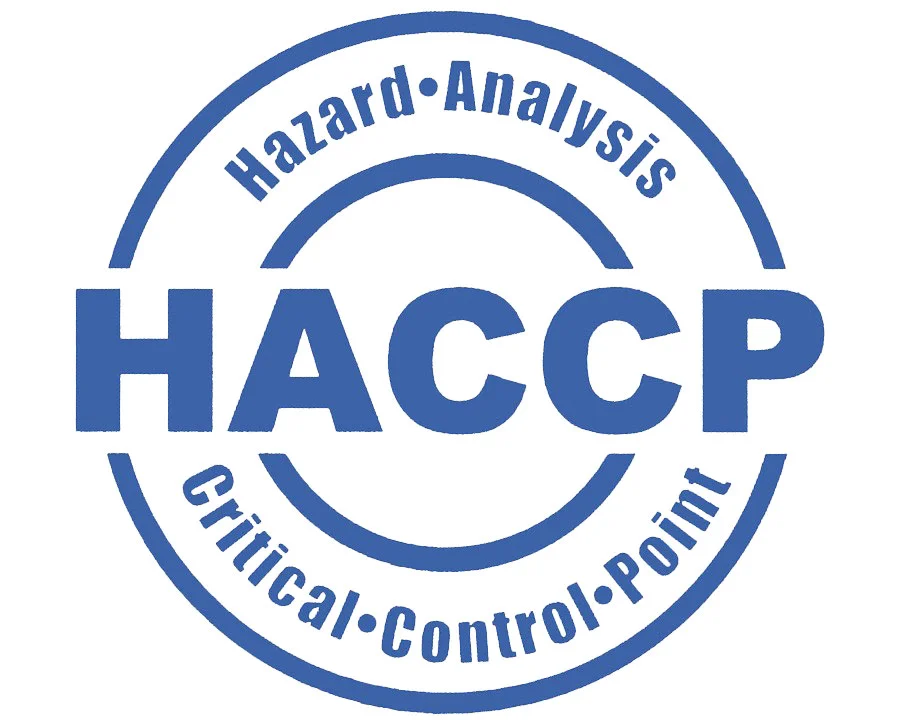
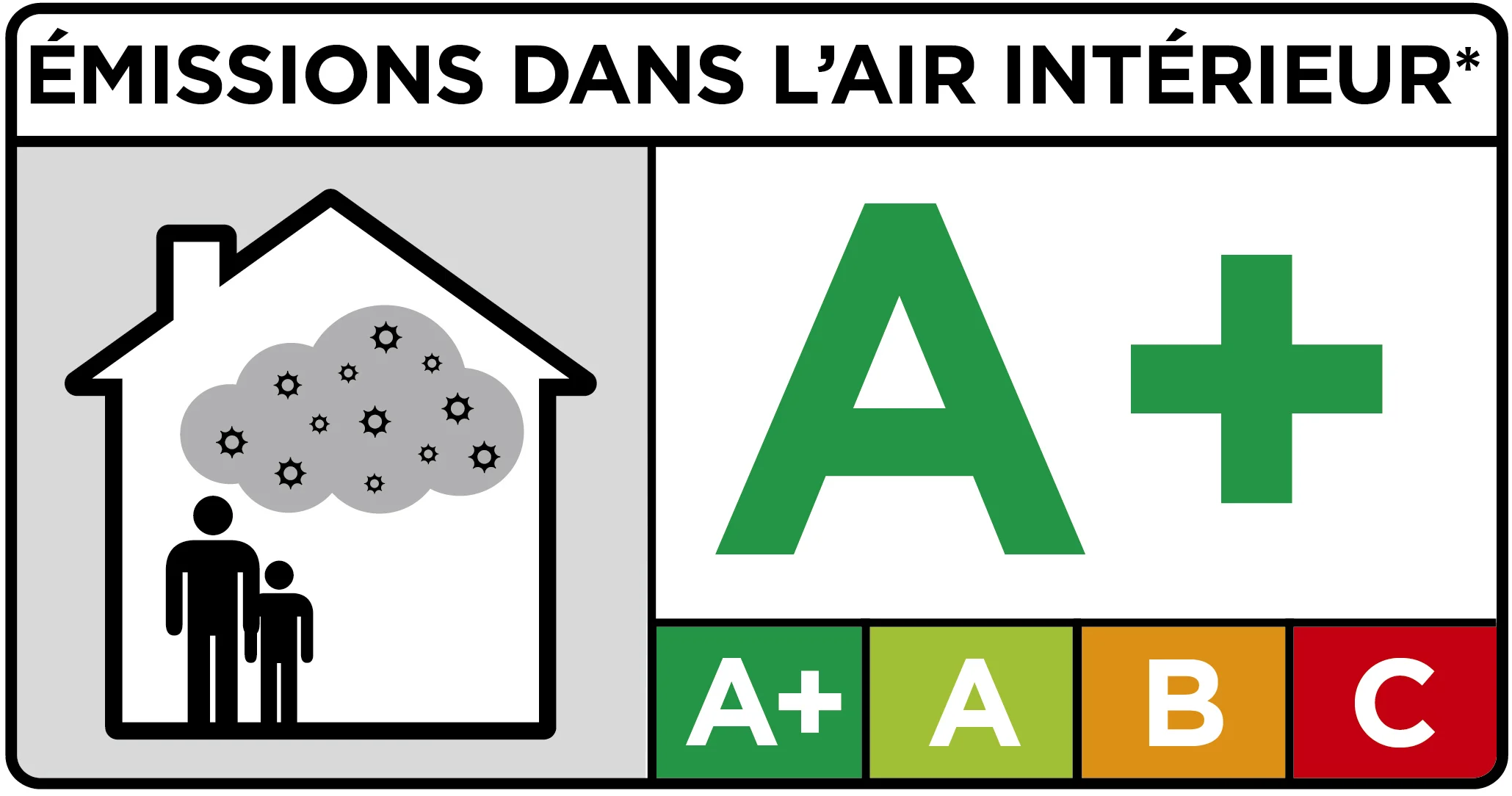
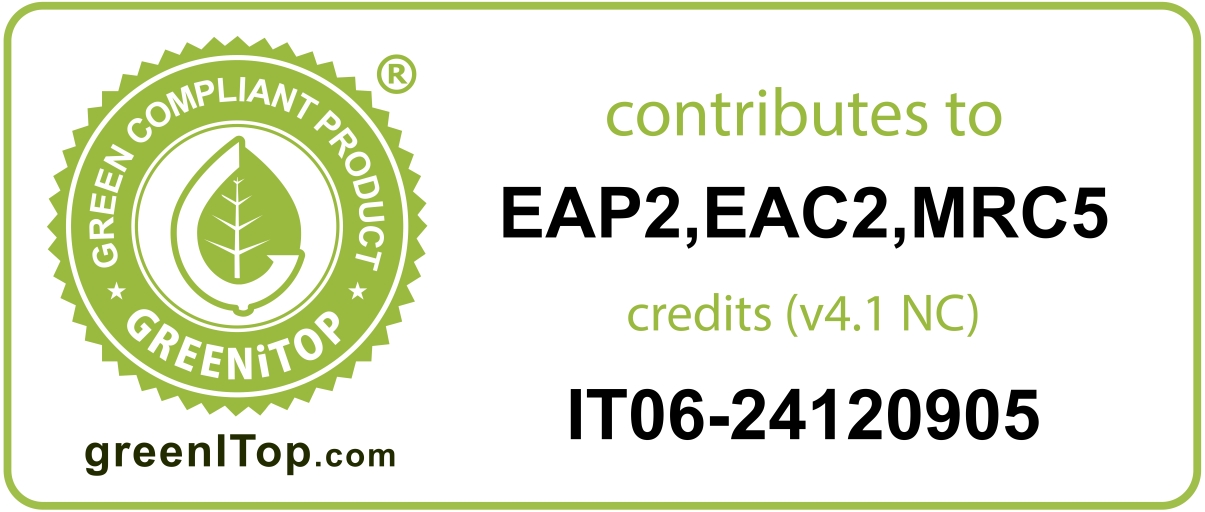
Descrizione
Finitura colorata a due componenti (A+B) a base di resine epossidiche ed amminiche in dispersione acquosa, ad alto contenuto di solidi.
Ottima resistenza all’usura.
Facile pulibilità e sanificabilità della superficie.
Buona resistenza all’acqua, alle soluzioni alcaline, a detersivi e ad idrocarburi, sia altobollenti che bassobollenti (olio, gasolio, benzina, ecc.).
PAVIWATER è idoneo per il rivestimento di pavimenti e pareti in ambienti con presenza di alimenti, sottoposte a valutazioni di sistema HACCP in conformità a Reg.852/2004 (D.Lgs.193/2007).
Il formulato è fornito in versione già colorata per alcune tinte o in versione non pigmentata (NP) con a parte COLORPASTA W.
Utilizzi
Verniciatura colorata di pavimenti in calcestruzzo all’interno di fabbricati.
Finitura per rivestimenti epossicementizi o epossidici a spessore.
Idoneo per ambienti alimentari, in quanto facilmente pulibile e sanificabile.
Rigenerazione della colorazione di pavimentazioni in resina.
Rivestimento per zoccolature di locali asettici nell’industria alimentare, farmaceutica, ospedali, aree pubbliche.
Supporto
Il sottofondo deve possedere una resistenza minima alla compressione di 25 N/mm2 e a trazione di 1,5 N/mm2 .
Preparazione del supporto
Fondi in cls dovranno essere solidi, asciutti (stagionati se di nuova costruzione), livellati, assorbenti, non inquinati da oli, detergenti, disarmanti, polveri od altre sostanze.
Valutare il tipo di preparazione meccanica più conveniente (abrasivazione o levigatura).
Eventuali buchi e lievi anomalie possono essere preventivamente riparati con PAVIRAPID o SIVITCOL.
Pavimenti piastrellati vanno abrasivati o levigati fino a superficie completamente opacizzata.
Rivestimenti in resina già esistenti vanno abrasivati o levigati, eliminando quindi i residui di polvere.
Superfici cementizie assorbenti o tendenti a sfarinare vanno prima trattate con PAVIWATER T68 o con una ripresa di PAVIWATER diluito con il 50% in peso di acqua.
I supporti preparati mediante levigatura che presentano segni di abrasione vanno rasati con formulati Sivit idonei.
Supporti umidi o soggetti alla risalita capillare di umidità vanno trattati con ECOFONDO (contattare l’Assistenza Tecnica Sivit).
Applicazione
PAVIWATER GIA' IN TINTA.
Al momento dell’applicazione unire i due componenti predosati in un unico recipiente. Miscelare con cura per 2 minuti, utilizzando adeguata attrezzatura (trapano con elica) e avendo cura di pulire con spatola le pareti dei contenitori al fine di miscelare tutto il prodotto.
Terminata la fase di miscelazione, rispettare il tempo di induzione* lasciando riposare il prodotto nella latta.
Aggiungere lentamente e sotto agitazione l’acqua di diluizione (consigliato 20% per la prima ripresa, 10% per la mano di finitura), rimescolare il prodotto per 1 minuto e applicare a rullo per un consumo di 0,130 kg/m2 per ciascuna ripresa.
PAVIWATER NP + COLORPASTA W.
Mescolare bene la pasta colorante per omogeneizzare eventuali sedementi.
Al momento dell'applicazione unire COLORPASTA W al componente A e miscelare con cura. Aggiungere poi il componente B e miscelare per 2 minuti, utilizzando adeguata attrezzatura (trapano con elica) e avendo cura di pulire con spatola le pareti dei contenitori al fine di miscelare tutto il prodotto.
Terminata la fase di miscelazione, rispettare il tempo di induzione* lasciando riposare il prodotto nella latta.
Aggiungere lentamente e sotto agitazione l’acqua di diluizione (consigliato 20% per la prima ripresa, 10% per la mano di finitura), rimescolare il prodotto per 1 minuto e applicare a rullo per un consumo di 0,130 kg/m2 per ciascuna ripresa
Per ottenere una superficie antiscivolo, aggiungere il 3-5% in peso di SFERETTE DI VETRO (FINI o GROSSE). Mantenere in agitazione il prodotto per evitare la sedimentazione.
PAVIWATER può anche essere applicato “a rasare”: in questo caso, aggiungere alla miscela il 30% in peso di SFERETTE DI VETRO GROSSE ed applicare con cazzuola americana, per un consumo massimo di 0,200 kg/m2 di PAVIWATER.
* PAVIWATER deve essere applicato entro il tempo di utilizzo e dopo il tempo di induzione in funzione della temperatura ambientale, si veda tabella a fondo scheda.
Avvertenze
Evitare di preparare miscele parziali di prodotto per non incorrere in accidentali errori, che potrebbero comportare un mancato o completo indurimento.
Se non si rispettano i tempi di induzione e di utilizzo, si può avere difformità della finitura, evidenziata da diverso colore e grado di lucido.
Come finitura va applicato a rullo uniformando la superficie con movimenti paralleli.
Per applicazioni a basse temperature è possibile diluire il formulato con una miscela 1:1 di acqua ed alcol etilico.
Proteggere il prodotto applicato da umidità, condensa ed acqua per almeno 24 ore.
Tonalità sul giallo, arancione o alcuni rossi possono richiedere più riprese per ottenere un buon effetto coprente (in alcuni casi si consiglia una prima ripresa aggiuntiva di colore bianco).
Diversi lotti di produzione del medesimo colore possono presentare piccole differenze: ove possibile utilizzare materiale proveniente da un unico lotto di produzione per ciascuna area da trattare.
Alcuni colori a base di pigmenti organici (rossi, blu, verdi, gialli intensi, …) tendono a cedere colore nel caso in cui siano sottoposti ad abrasione (a secco o a umido): in questi casi si consiglia di proteggere il colore con una ripresa di finitura trasparente (della serie FINIWATER o FINISOL).
Non applicare su intonaci a base gesso destinati ad ambienti umidi (ad es. docce).
Specifiche tecniche
DATI PRODOTTO | |
---|---|
Colore | A richiesta secondo cartella colore |
Consumo | 0,130 kg/m2 |
Peso specifico (a 25°C): miscela (A+B) parte A parte B | 1,48 +/- 0,05 g/ml 1,55 +/- 0,05 g/ml 1,10 +/- 0,05 g/ml |
Viscosità (a 25°C): miscela (A+B) miscela (A+B) diluita al 10% | 3.500-4.000 mPa•s (spindle 2, rpm 5) 800-1.300 mPas•s (spindle 2, rpm 5) |
Residuo secco (A+B) | 69% in peso e 54% in volume |
VOC pronto uso (D.lgs 161/06) | < 50 g/l Cat.A/j. Pittura bicomponente ad alte prestazioni (BA) |
Punto di infiammabilità | Non applicabile |
Solvente per la pulizia attrezzi | Acqua |
Magazzinaggio | 12 mesi, conservare in luogo asciutto ad una temperatura compresa tra i 10°C ed i 35°C |
DATI APPLICAZIONE E TEMPI | |
---|---|
Rapporto di miscela (in peso) | Versione già in tinta: A=100, B=28 Versione NP: A=85, pasta=15, B=28 |
Tempo di induzione | 10 min (30°C) 15 min (25°C) 25 min (15°C) |
Pot-life (50% U.R.) | a 15°C 130 min a 25°C 105 min a 30°C > 80 min |
Secco al tatto (50% U.R.) | a 15°C 18-22 ore a 25°C 4-6 ore a 30°C 2,5-3,5 ore |
Pedonabile (50% U.R.) | a 25°C da 14 a 36 ore |
Ricopertura (50% U.R.) | a 25°C da 14 a 36 ore |
Trafficabile (50% U.R.) | a 25°C 3 giorni |
Indurimento in profondità (50% U.R.) | a 25°C 7 giorni |
Condizioni ambientali d’uso | Temperature comprese tra i +15°C e i +35°C, U.R. < 70% (*) |
Temperatura superficie | Tra i +10°C e i +30°C |
Manutenzione rivestimento | Per le operazioni di pulizia utilizzare detergenti neutri |
DATI TECNICI PRESTAZIONALI | |
---|---|
Aspetto | Superficie leggermente bucciata |
Gloss (60°) | 60-65 Il grado di brillantezza del prodotto PAVIWATER applicato è influenzato da diversi fattori: temperatura del materiale, umidità ambientale, temperatura di applicazione e porosità del supporto. |
Resistenza all’abrasione norma UNI 8298-9 | 55 mg (TABER Mola CS-17-1000 giri -1000 g di peso) |
Reazione al fuoco (UNI EN 13501-1:2007) | Bfl -s1 |
Scivolosità (D.M.236/89) | µ>0,40 (con 3% di SFERETTE DI VETRO FINI) |
Resistenze chimiche | Contattare il Servizio Tecnico Sivit per informazioni dettagliate |
MARCATURE CE | |
---|---|
Marcatura CE (reg. n. 305/2011) | Conforme a EN I504-2. Rivestimento(C) Principio (PR) |
Adesione Pull Off (EN 1542) | 3,6 MPa |
Resistenza all'abrasione norma EN 5470-1 | 84 mg |
Resistenza all'urto (EN 6272-1) | 11,8 N•m (Classe 2) |
Permeabilità all'acqua (EN 1062-2) | w 0,012 kg/(h0,5 m2) |